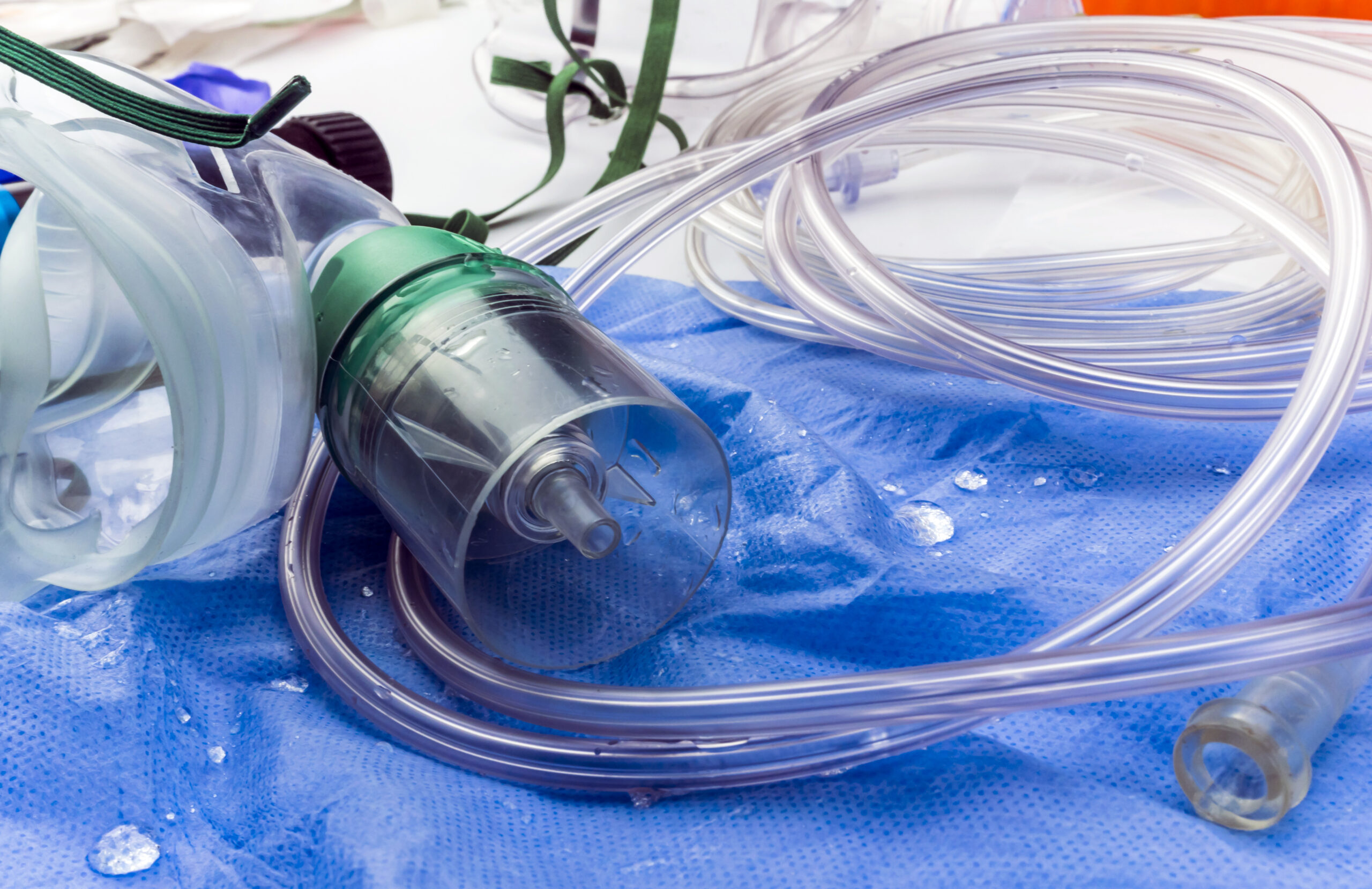
Why Liquid Silicone Rubber Is the Material of Choice in Medical Manufacturing
Medical device production is highly regulated and constantly changing. Because of this, materials must do more than just “work”. It’s vital that they perform with consistency, meet strict compliance standards, and support innovative product design. That’s why liquid silicone rubber (LSR) has become the material of choice for medical manufacturing.
From medical implants and drug delivery devices to wearable monitors and surgical components, LSR is helping manufacturers push the limits of what’s possible in healthcare. Here’s why:
1. Why LSR is Trusted Across Multiple Medical Sectors
Liquid silicone rubber has exceptional versatility, making it suitable for a wide range of applications:
- Implantable devices that require long-term biocompatibility
- Wearables and diagnostic tools that need skin-safe materials
- Surgical and dental components that demand precision and durability
- Sealing and gasketing solutions for fluid and air control in devices
Whether it’s a Class I product or a more complex Class III medical device, LSR can be customized to meet the needs of the application.
2. Built-In Compliance for Safety and Performance
Medical manufacturing comes with a tight web of regulatory expectations. LSR is a compliant material by design:
- It meets or exceeds FDA and USP Class VI standards
- It performs consistently under ISO 10993 biocompatibility testing
- It is compatible with sterilization methods like steam autoclaving, gamma radiation, and ethylene oxide (EtO)
With LSR, medical manufacturers can reduce risk during product development and speed up time-to-market with confidence.
3. High Precision for High-Volume Production
One of the greatest strengths of liquid silicone rubber is its compatibility with liquid injection molding (LIM). This process allows for:
- Tight tolerances and repeatable results
- Complex part geometries and undercuts
- Flashless molding that minimizes secondary operations
- Relatively fast cure times
- Automation potential for efficient, scalable production
In other words, LSR isn’t just good for prototypes—it’s built for production.
4. Long-Term Durability for Critical Applications
In medical use, failure is not an option. LSR maintains its properties over time, even under extreme conditions:
- Heat-resistant up to 200°C and beyond
- Chemically stable in contact with body fluids and cleaning agents
- Resilient and flexible even after thousands of cycles or sterilizations
Whether in the body, on the body, or in the surgical suite, liquid silicone rubber holds up under pressure.
5. Ideal for Customization and Rapid Development
LSR is also a favorite among engineers because of how easily it can be customized:
- Tailored durometers (softness/hardness) to fit the application
- Color matching for brand or function-specific identification
- Custom tooling and mold design for unique device needs
- Rapid prototyping to iterate designs quickly and affordably
This makes LSR a powerful partner for teams innovating at the cutting edge of medical technology.
Partner With Gulf for Your Next LSR Medical Manufacturing Project
As medical device manufacturers face increasing pressure to deliver safer, smarter, and more patient-friendly products, the materials they choose matter more than ever. Liquid silicone rubber isn’t just a material, it’s a manufacturing advantage.
At Gulf, we specialize in custom engineered rubber and plastic solutions, including expert liquid silicone rubber medical manufacturing. Whether you’re refining an existing product or developing something brand new, our team is here to help bring your vision to life.
Start your next project with Gulf today!