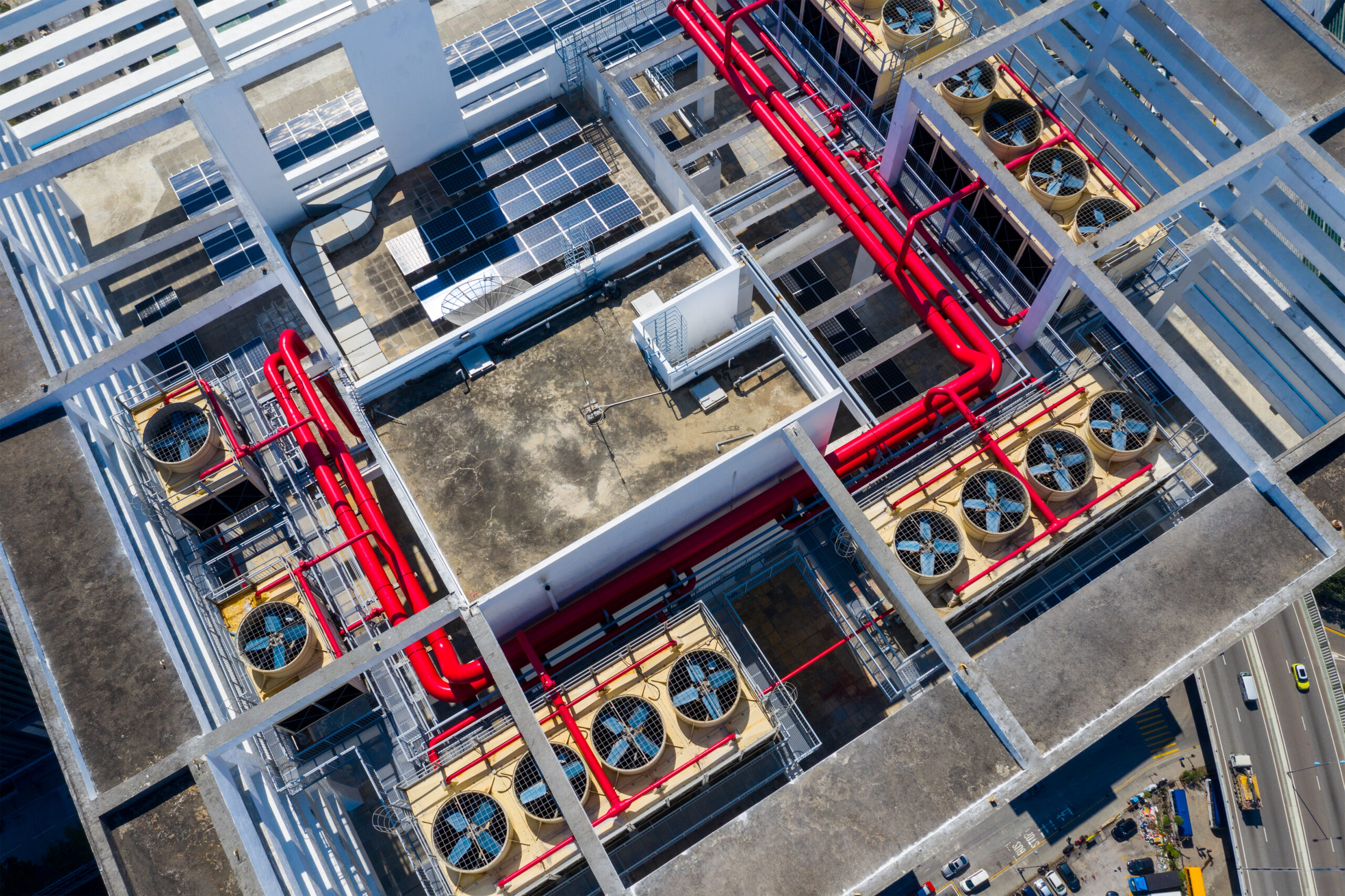
The Pressure Switch Diaphragm: Benefits, Challenges, and Industry Applications
Pressure switch diaphragms are critical components in the HVAC, automotive, appliance, medical, and irrigation markets, to name a few. As a leading pressure switch diaphragm manufacturer, we’ve worked on hundreds of projects and have extensive experience with the complex and nuanced design requirements, as well as the need to meet strict industry standards. If you’re a product developer who is researching which type of diaphragm to use in your next project, take a moment to explore the benefits and challenges of selecting a pressure switch diaphragm for your project.
What is a Pressure Switch Diaphragm?
A pressure switch diaphragm is a flexible membrane-like component that is used within a pressure switch system to monitor and respond to changes in pressure. The diaphragms typically separate two chambers within a switch, and when the pressure gets to a certain threshold, the diaphragm flexes and triggers a mechanical or electrical switch. When the pressure normalizes, the diaphragm goes back to its original position and resets the switch. Think of sensing the water level in your washing machine, monitoring tire pressure in your car, or regulating water flow from faucets and shower heads in your home. In each of these applications, a pressure switch diaphragm is used to monitor pressure, trigger activation, and reset when the pressure reaches the desired level.
Flexibility and durability are the two most important features of a pressure switch diaphragm. They’re often made from EPDM, NBR, silicone, or other elastomers. Depending on the application, they can also be reinforced with fabric for additional durability. What makes them so unique is their resistance to chemical and environmental conditions.
Benefits of Pressure Switch Diaphragms
Understanding the benefits of pressure switch diaphragms will help us figure out if this component is the right fit for your project. Do you need a component that has enhanced sensitivity, is durable, customizable, has a compact design, and is affordable? If so, then you may be in the right place.
Enhanced Sensitivity: The main responsibility of this type of diaphragm is to respond to subtle changes in pressure to control fluid flow or switch activation in your application. It does so with precision geometry of the diaphragm.
Durability: For pressure switch diaphragms to operate at peak performance, they need to be made of high-performance elastomers, including overmolding on substrate and reinforced with fabric. This makes them extremely durable.
Customizability: As a pressure switch diaphragm manufacturer, we understand that your application has its own set of standards and requirements. Gulf can customize by pressure range, temperature tolerance, and material compatibility. However strict or precise the specifications, we can customize the diaphragm to meet your needs.
Compact Design: With the miniaturization of products across many industries, pressure switch diaphragms are in high demand for many projects because of their ability to fit into compact designs. Medical devices, such as CPAP machines and oxygen concentrators, are great examples of compact applications that utilize pressure switch diaphragms.
Cost-Effectiveness: Pressure switch diaphragms have a long lifespan with a low production cost. This means system efficiency over time is high while budgets can remain cost effective.
Challenges When Using Pressure Switch Diaphragms
When working with a pressure switch diaphragm manufacturer, it’s important to also understand the potential material challenges. As pressure switch diaphragm manufacturers, it’s our process to review all aspects of a component so our clients understand all features, benefits, and challenges. We work together to weigh the pros and cons, and select the best fit material for every project.
Material Selection: Once we review your project specifications, we move to material selection. We say this is one of the most critical steps in the manufacturing process given the material selected needs to be compatible with your product. Will it need to be compatible with fluids, gasses, handle environmental conditions, etc.? We spend a lot of time on this step as it can be challenging to nail down the best suited material that meets all requirements.
Performance Under Extreme Conditions: While pressure switch diaphragms can withstand harsh conditions, extreme conditions require extra attention. It is very important that the diaphragm maintains its integrity for the operation of the switch. There are advanced formulas we use that are made for these types of situations and can handle the extremes.
Degradation Over Time: As with any component, a pressure switch diaphragm may degrade over time, especially if exposed to harsh or extreme conditions. To ensure the longest lifespan possible, we treat materials with protective coatings. Maximizing your product’s reliability, durability, and performance is our main goal.
Balancing Flexibility and Strength: Balancing flexibility and strength as a pressure switch diaphragm manufacturer can be challenging; however, our years of experience and on-site engineers are here to design the component with the right flexibility and maximum strength needed for your product to operate efficiently.
Pressure Switch Diaphragm Applications
We have worked across many diverse industries to provide the highest quality pressure switch diaphragms for our customers. Industries and applications that use pressure switch diaphragms include:
Automotive: Fuel systems, brake systems, and emission control systems
HVAC: Pressure monitoring in heating, ventilation, and air conditioning systems
Industrial Equipment: Compressors, pumps, and hydraulic systems
Medical Devices: Oxygen concentrators, ventilators, and diagnostic equipment
Agriculture: Irrigation systems and precision planting equipment
Food and Beverage: Sanitary pressure control in processing and packaging systems
Why Choose Us as Your Pressure Switch Diaphragm Manufacturer?
Gulf has extensive experience in pressure switch diaphragm manufacturing. Partnering with us means you can expect research-driven material selection, a diaphragm designed to your specifications, custom engineering, rigorous testing, a product that exceeds industry standards, and optimal performance in your application. We’re here to help. Give us a call today so we can learn more about your project.