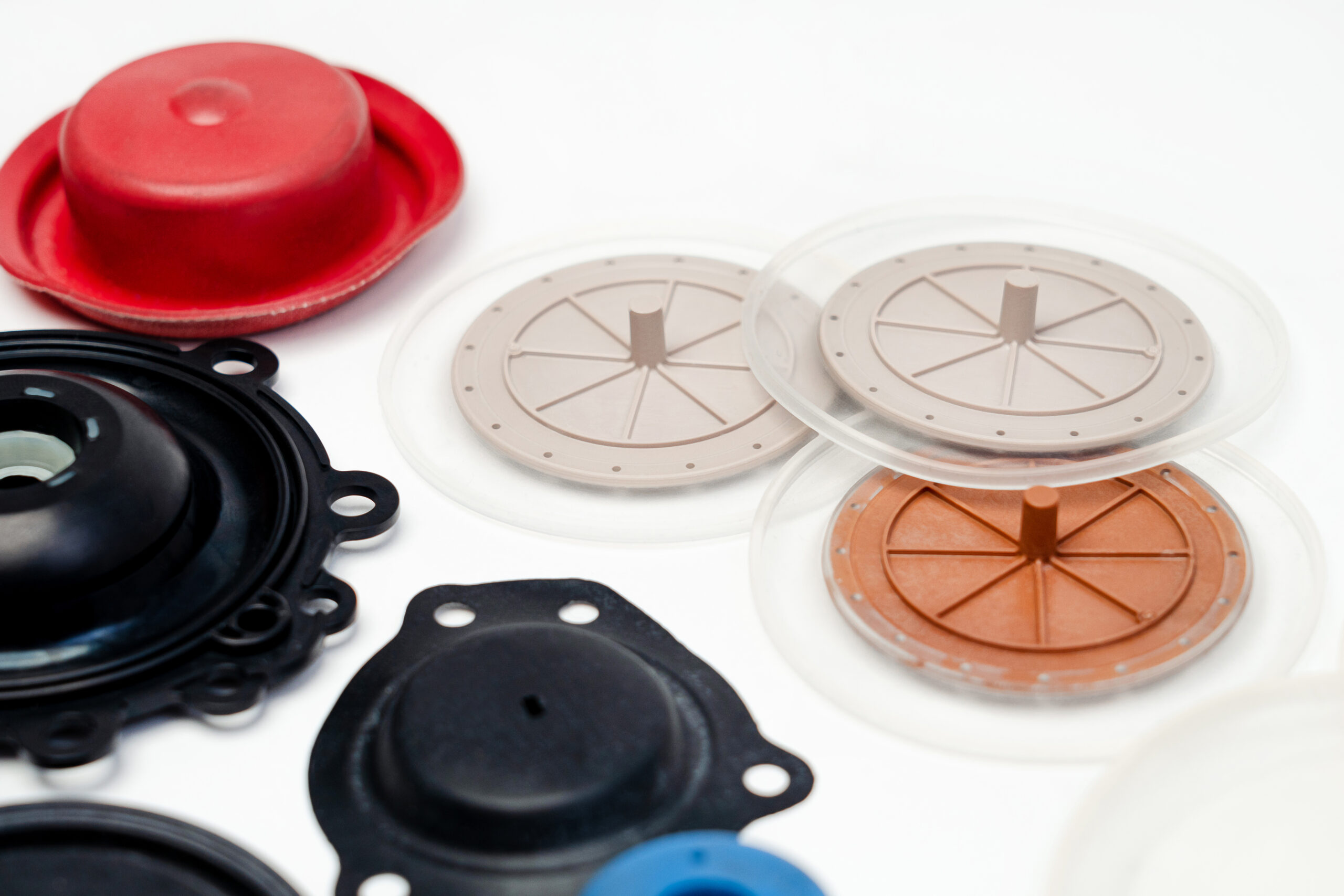
The Power of Fabric Reinforced Diaphragms: Benefits, Challenges, and Future Innovations
As a leading manufacturer of fabric reinforced diaphragms, our expert engineers at Gulf Engineered Rubber and Plastics Solutions (Gulf) understand how essential these components are across various industries. The goal of these flexible diaphragms is to transmit pressure and force between two sides of a valve, pump, regulator, switch, actuator, stabilizer, or other relevant components.
Fabric reinforced diaphragms are made by molding and attaching a fabric insert to a piece of rubber providing a flexible barrier between a moving and stationary part. The fabric reinforcement makes the diaphragm more durable, flexible and resistant to wear and tear. Below, our engineers explore the benefits of fabric-reinforced diaphragms, the challenges faced in their manufacturing, and the emerging innovations that are shaping the future of this technology.
Benefits of Fabric-Reinforced Diaphragms
Durability and Strength
One of the biggest advantages of fabric reinforced diaphragms is that they’re very durable and strong. The added fabric layer allows the diaphragm to withstand high pressures and more extreme operating conditions compared to non-reinforced diaphragms. Adding this fabric layer also helps prevent the diaphragm from becoming deformed or misshaped in these high pressure environments, which helps the product have a longer life span.
Flexibility and Precision
Fabric-reinforced diaphragms are unique because they can incorporate both flexibility and precision without having to sacrifice either. In fact, since these types of diaphragms are so flexible, they’re able to maintain their strength in tight tolerances and provide precise control in mechanical systems. This balance of strength and flexibility makes them the ideal component for applications where precise movement is crucial, such as in actuators and precision pumps.
Chemical and Environmental Resistance
Fabric-reinforced diaphragms have great resistance to a wide range of chemicals and environmental factors. Additionally, manufacturers have the ability to customize the diaphragm to meet specific industry needs by selecting the type of fabric and elastomer material to be used. By creating these unique diaphragms, we can ensure the component withstands exposure to harsh chemicals, extreme temperatures, or even UV radiation. This makes them suitable for various industries such as chemical processing, oil and gas, and wastewater treatment where applications encounter aggressive substances and harsh conditions.
Challenges in Manufacturing Fabric-Reinforced Diaphragms
Complexity in Production
Manufacturing fabric-reinforced diaphragms is a complicated process, which is why it’s important to partner with a reliable manufacturer. When shopping around, look for a manufacturer who values quality and precision to ensure the attachment of the fabric and the elastomer is flawless. If not, there could be weak points or inconsistencies in the final product. Due to the required precision when manufacturing these diaphragms, there may be longer production times or higher costs – especially for custom solutions that need certain materials or unique designs. Partnering with the right manufacturer will help ensure all expectations, timelines, and budgets are discussed prior to, and throughout, the production process.
Cost Considerations
As mentioned in the previous section, manufacturing fabric-reinforced diaphragms can be more expensive than standard diaphragms. This is because of the required additional materials and labor involved during the production process. The cost of high-quality fabrics, advanced elastomers, and the intricate manufacturing processes can be weighed against the benefits these diaphragms offer. For many applications, the higher initial cost is justified by the extended lifespan and improved performance that fabric-reinforced diaphragms offer.
Design Limitations
When designing a fabric-reinforced diaphragm, it’s important to consider the application in which it will be used. The materials selected during the design phase must match the intended use as not all fabrics and elastomers are compatible with every application. Also, something else to consider are limitations in overall thickness. Adding a layer of fabric will change the thickness of the diaphragm, which can be a positive or negative change depending on the intended use. In general, be sure to discuss the requirements and details of the fabric-reinforced diaphragm before entering the design phase with a manufacturer.
Future Innovations and Trends
Advanced Materials
Everyday there is more research on new fabric and elastomer combinations that can withstand higher pressures, hotter temperatures, and highly aggressive chemicals. As new materials are introduced, there will be even more opportunities for greater performance characteristics. These innovations will allow for fabric-reinforced diaphragms to be used in industries that were previously limited.
Sustainability and Eco-Friendly Solutions
There are many industries that prefer, and oftentimes require, finding eco-friendly solutions to help better the planet. We’re also seeing a prioritization of sustainability in business operations with more advanced applications and machinery. Due to this, many quality manufacturers are following these trends by experimenting with the use of biodegradable elastomers and recycled fabrics to develop fabric-reinforced diaphragms. The challenge is making sure the end result meets environmental standards without compromising performance. In the near future, it is likely we will see more sustainable solutions and options as companies seek to reduce their environmental footprint.
Integration with Technology
In recent years, there has been an introduction of smart technology into fabric-reinforced diaphragms. For example, some manufacturers have embedded sensors within the diaphragm material to monitor performance in real time. These sensors typically track pressure, temperature, and wear on the diaphragm. This information is then used to optimize system performance, predict maintenance needs, and overall help extend the lifespan of the diaphragm.
Work With Gulf to Design and Develop Your Fabric-Reinforced Diaphragms
The combination of durability, flexibility and chemical resistance the fabric-reinforced diaphragms offer is hard to match. They continue to be a crucial component in a wide range of applications for various industries. Furthermore, with ongoing advancements in materials and technology, we can expect these diaphragms to continue to evolve and remain an important component for many applications and industries. Our expert team of engineers encourage continued research and experimentation in this field as we work together to try to unlock even greater potential of fabric-reinforced diaphragms.
For more information on custom rubber and plastic solutions, or to discuss your specific needs, contact our Gulf Rubber team today. We’re here to help you find the perfect solution for your application needs.