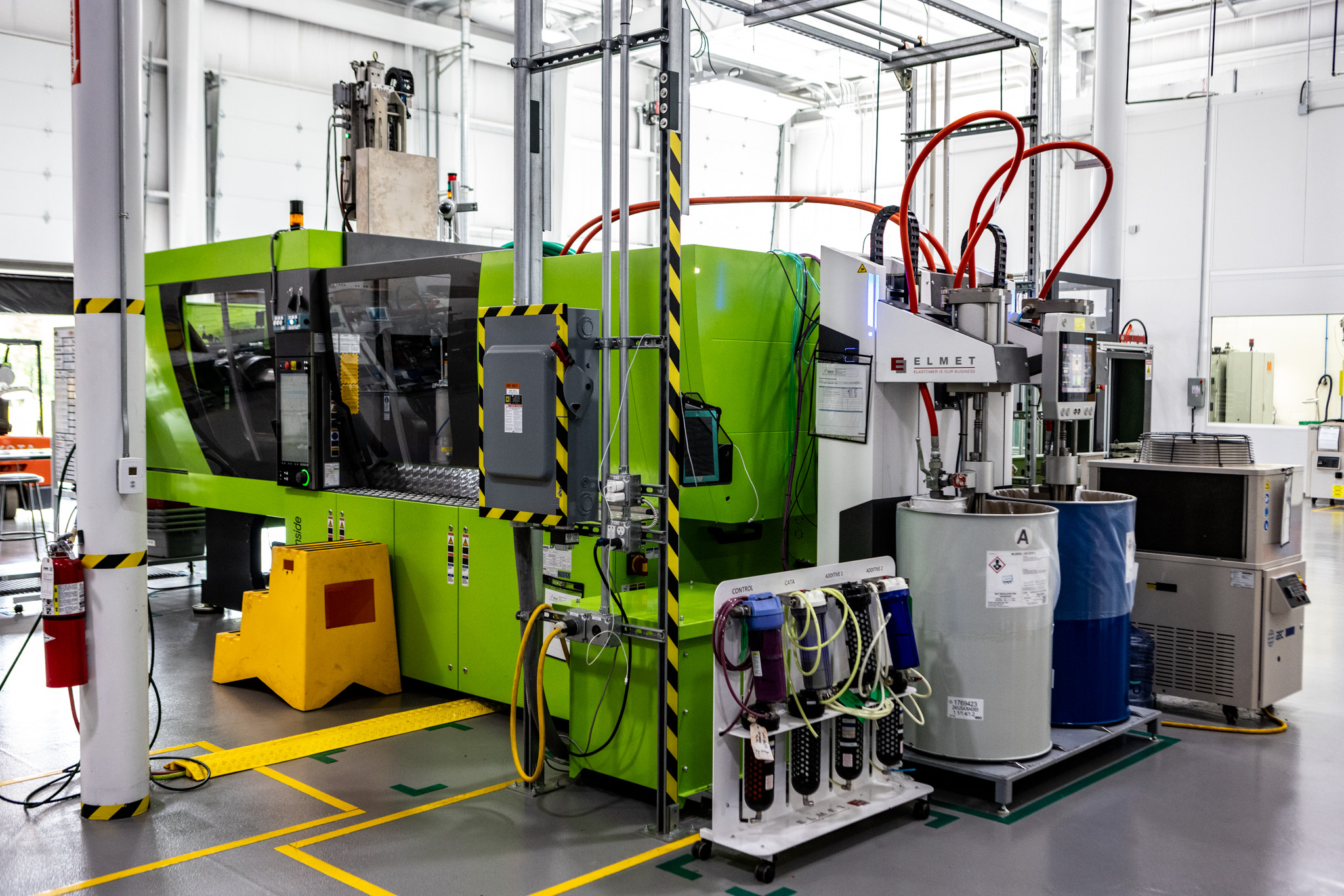
Medical Device Component Manufacturing: Exploring Quality, Process, And Compliance
Medical device component manufacturing must adhere to the highest industry standards for the safety of both practitioners and their patients. To meet these exacting standards, healthcare providers in hospitals and private practices require top-tier rubber and plastic components for their medical devices. Partnering with a trusted provider like Gulf Engineered Rubber and Plastics Solutions (Gulf) ensures that these components undergo rigorous testing, are produced efficiently, and can be customized to meet specific life saving requirements. Below, our expert engineers explore the quality, manufacturing processes, and quality assurance measures shaping the production of medical device components.
Quality Medical Device Component Manufacturing
Biocompatibility
In medical device component manufacturing, it’s important to think about quality given its intended use. Often, these devices will be used with human tissue and fluids, so biocompatibility of the medical device component is vital. Both rubber and plastic materials can be formulated to resist degradation which is important for safety during use. Additionally, their ability to resist bacteria growth and ease of sterilization make them ideal for maintaining a sterile environment. Some examples where medical-grade rubber and plastic components are used include surgical tubing, catheters, seals, and gaskets where prolonged contact with the body is common.
Precision Engineering
In medical device manufacturing, the quality of precision engineering is key. Whether it’s creating tiny valves for IV pumps or custom gaskets for surgical instruments, rubber and plastic components may need to be molded and engineered to incredibly tight tolerances. The flexibility of these materials also allows for complex geometries and designs, supporting the functionality of intricate medical device components. At Gulf, we pride ourselves on utilizing advanced technologies to ensure that every component meets the exact specifications needed for safe, effective performance.
Customization
Being able to customize solutions for specific medical needs is a requirement for any medical device component manufacturer. From personalized prosthetics to custom-fitted implants, the possibilities are endless. Ensuring quality in customization is crucial, as it directly impacts patient outcomes, safety, and long-term device performance.
Medical Device Component Manufacturing Processes
At Gulf, we use a variety of cutting-edge manufacturing processes to create high quality rubber and plastic medical device components. We use a handful of different manufacturing processes and technologies so our team can offer unique, tailored benefits depending on the application. This approach ensures that each component not only meets the specific needs of the medical device but also adheres to stringent industry standards for performance and reliability.
Over-Molding
Over-molding is a process where one material, typically a soft elastomer, is molded over a rigid substrate. This is commonly used in medical devices where grip and comfort are important, such as handles on surgical tools. Over-molding can also improve functionality by creating seals or barriers between different materials which ensures the devices are sterile and safe for critical medical environments.
Compression Molding
Compression molding involves placing rubber or plastic material into a heated mold where pressure then shapes it into the desired form. This process is ideal for creating high strength, durable components that are more resistant to wear and tear. Medical seals, gaskets, and other components that require long-term reliability are often produced through compression molding.
Extrusion
Extrusion is commonly used to create continuous lengths of rubber or plastic tubing, which are essential in many medical devices like catheters, feeding tubes, and IV lines. The process allows for tight control over the thickness and diameter of the tubing, making sure there is consistent quality across production runs.
Injection Molding
Injection molding is one of the most versatile and widely used manufacturing processes for creating medical device components. By injecting molten rubber or plastic into a precision mold, manufacturers can create complex shapes with high accuracy. This process is typically used to manufacture everything from small surgical device components to housings for diagnostic equipment.
Quality Assurance & Compliance in Medical Device Component Manufacturing
When it comes to medical device component manufacturing, there can be no margin of error. At Gulf, we follow the highest standards of quality assurance and compliance to guarantee that every component we design and engineer meets industry requirements.
Material Testing
Before production of a medical device component begins, a reliable manufacturer will test all materials to make sure they meet the necessary biocompatibility and durability standards. This can include chemical, thermal, and mechanical tests to confirm that the material can withstand the conditions it will be exposed to in medical settings.
Inspection
During the manufacturing process, our Gulf team will regularly do inspections to check that the medical device components meet specific design requirements and quality standards. These tests can be visual inspections or a form of automated testing. Both are performed to help identify any potential defects early in the process.
Final Testing
Before shipping any product, our engineers perform final testing to confirm that every component is safe, effective, and compliant. This includes functional testing to ensure the component performs as expected in real-world conditions.
Your Trusted Medical Device Components Manufacturer
At Gulf Engineered Rubber and Plastics Solutions, our commitment to quality is reflected in every step of our production process, from the selection of materials to final testing. We deliver components that meet the stringent requirements of the medical industry with a focus on tailored solutions, and rigorous quality assurance. This ensures Gulf provides healthcare providers with reliable, high-performance components that are critical for life-saving medical devices. Contact our expert medical device component manufacturing team to discuss your next project.