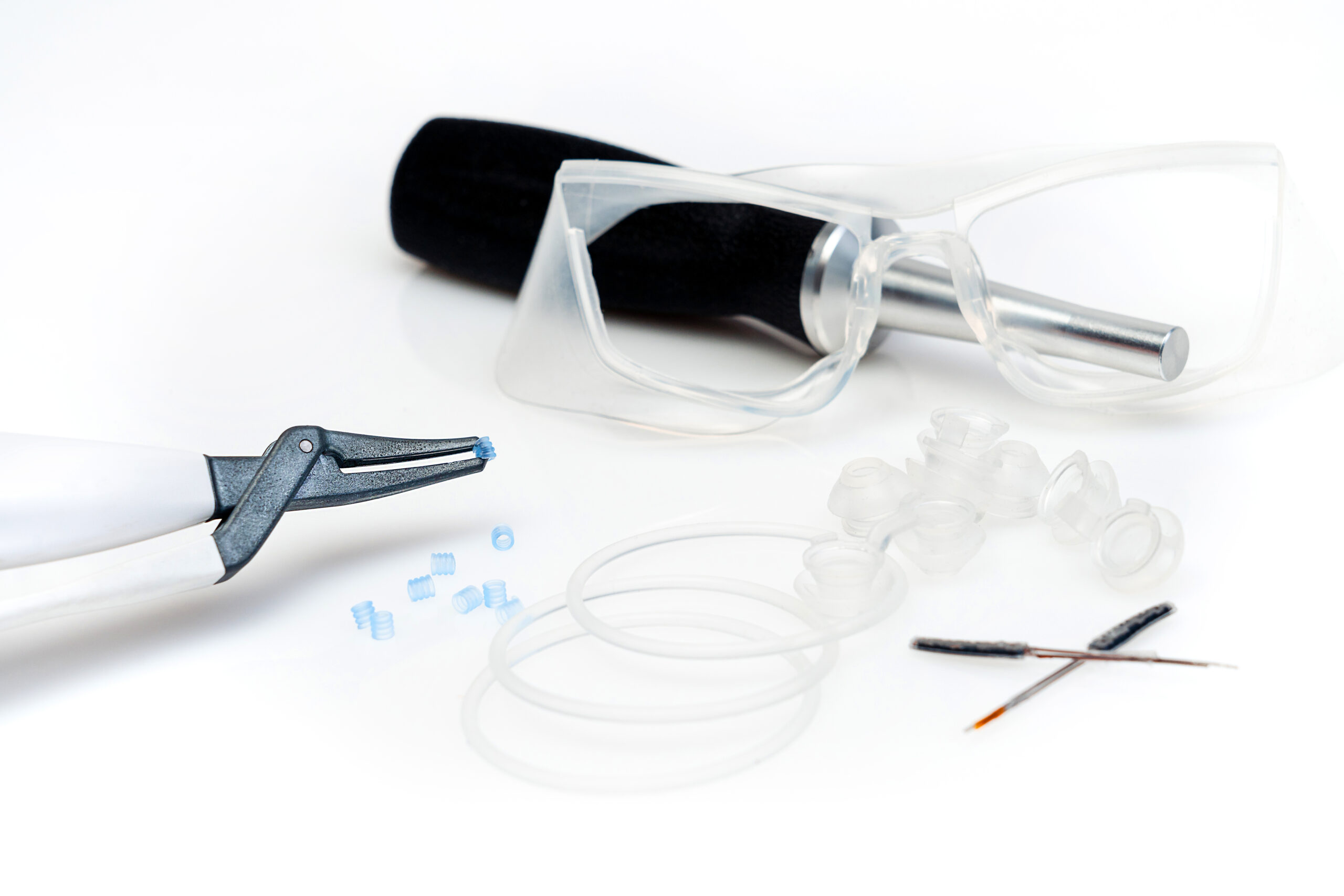
Liquid Silicone Rubber Medical Manufacturing: Setting the Standard for Quality Assurance and Innovation
Emerging as a game-changer in medical manufacturing, liquid silicone rubber has unique properties that make it ideal for many medical applications including intricate catheters, implants, surgical instruments, valves, seals and gaskets, and more. This means uncompromising quality standards, continuous improvements, and innovation for liquid silicone rubber medical manufacturing. Each step of the manufacturing process is intricate and must adhere to some of the strictest industry standards to ensure efficient healthcare solutions and provider and patient safety.
In this blog we’ll dive into quality assurance in the liquid silicone rubber medical manufacturing process and the future of this sought after material.
Validating the Integrity of the Raw Material
The quality journey begins with the selection of raw materials. In liquid silicone rubber medical manufacturing, it’s imperative to source the highest quality elastomers. The material testing before the product manufacturing process begins is rigorous. As a liquid silicone rubber manufacturer, we are testing for consistency, flow and cure characteristics, physical properties, and temperature and chemical resistances as well as purity, biocompatibility, and cytotoxicity with testing to certify compliance to standards such as United States Pharmacopeia (USP) Class VI and/or ISO 10993. Advanced testing techniques such as spectroscopy, rheology analysis, tensile testing, compression set, fluid resistance, and dimensional inspection are used to verify product integrity and functionality.
Quality Assurance for the Manufacturing Process
Once a raw material is selected, we move to the liquid silicone rubber medical manufacturing process. Given its unique characteristics, liquid silicone rubber has the ability to be molded and shaped, customizing its form and use for each complex design. This requires high levels of manufacturing precision including control over temperature, pressuring, and curing times. These measures are in place to ensure there is no deviation from required specifications and uniformity throughout the batch.
Manufacturer Compliance with Regulatory Standards
Given the strict regulation over the medical industry, it is not a surprise we see regulatory standards in liquid silicone rubber medical manufacturing. The myriad of regulations include the ISO 13485, FDA guidelines, and EU medical device directives. These regulations make sure that manufacturers like ourselves are on top of documentation, conducting regular audits, and staying abreast of evolving regulatory requirements to make sure that compliance is ongoing.
Innovation and the Future of Liquid Silicone Rubber
The rise in successful use and application of liquid silicone rubber has driven advancements in material science, manufacturing technologies, and market demand for innovation. In the manufacturing space, we are seeing innovations including enhanced properties, micro-molding, and sustainability as an inorganic elastomer that is not dependent on fossil fuels. In fact, silicone can be made from quartz (i.e. Silicon Dioxide) or even sand, which is an abundant resource.
New material properties are always top of mind when we think of innovation and liquid silicone rubber medical manufacturing. Advanced material formulations allow for a more durable product including higher tear strength, elongation, and heat resistance.
Micro-molding is on the top of the list for many manufacturers’ processes including liquid silicone rubber for medical manufacturing. With every medical device going miniature, we’re constantly innovating new ways for functionality and precision to remain the same but at a smaller scale.
Another emerging trend is smart silicone rubber where sensors and electronics are embedded into liquid silicone rubber components to provide sensing, monitoring, and feedback capabilities. We may see this innovation in wearable devices for real time data collection and analysis.
Sustainability is also the future of liquid silicone rubber. There has been interest in advanced technologies that develop recyclable and sustainable liquid silicone rubber for medical manufacturing. This will reduce the environmental impact and support sustainability initiatives across the nation.
Contact Gulf US for More Information About Liquid Silicone Rubber Manufacturing
Liquid silicone rubber has revolutionized medical manufacturing, offering unparalleled versatility, biocompatibility, and performance. With the widespread use comes an uncompromising commitment to quality and upholding manufacturing standards.
Quality assurance for liquid silicone rubber medical manufacturing is ongoing and is always improving. As manufacturers, we are constantly thinking of ways we can improve the quality assurance process to provide the highest quality product on the market. Gulf is dedicated to making sure that providers and patients receive safe and reliable products that will make a difference in their jobs and their health.