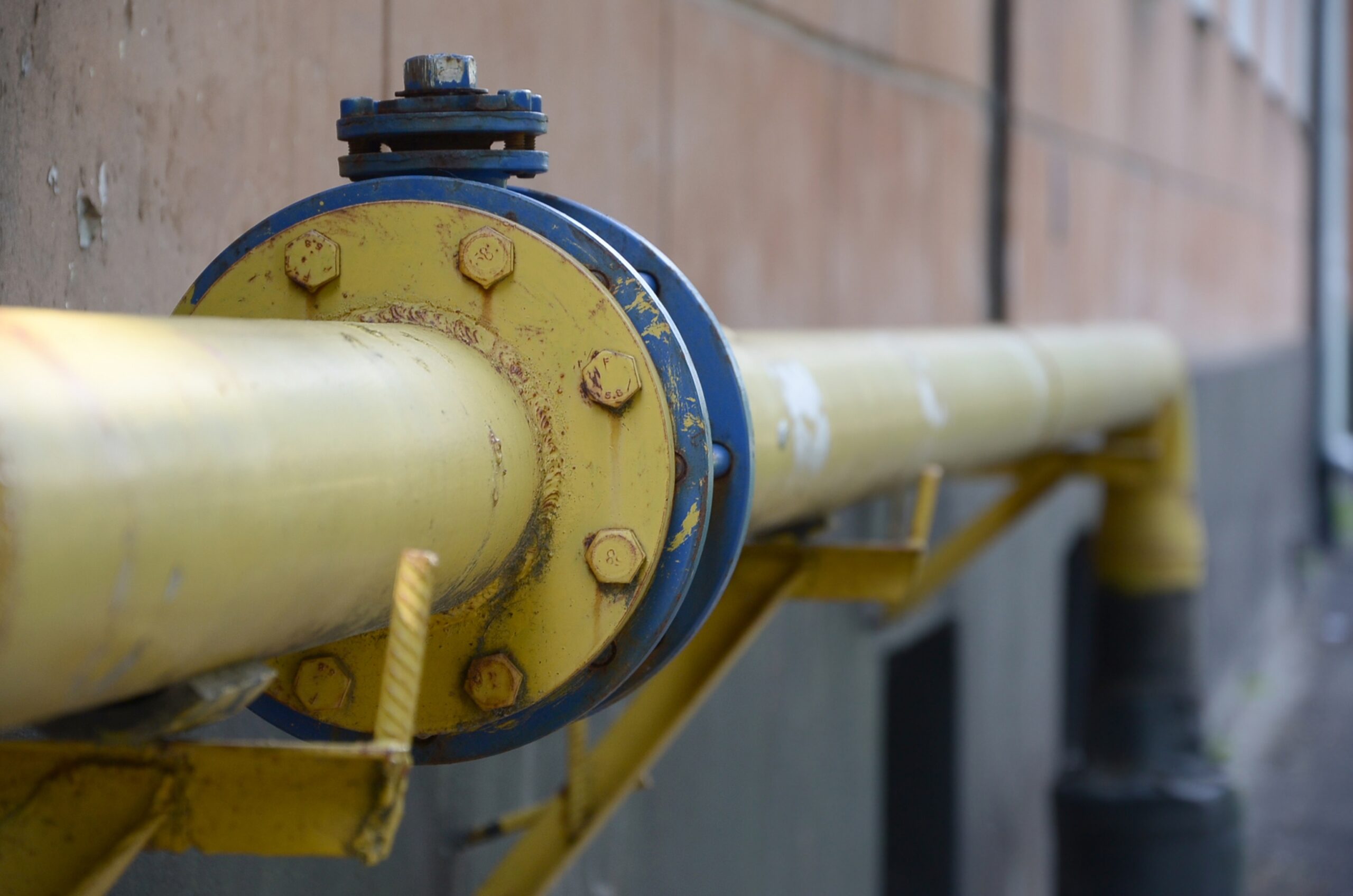
Common Challenges a Pipe Gasket Manufacturer Solves for Industrial Clients
In industrial settings, piping systems keep operations running by transporting everything from water and chemicals to oil and gas. However, these systems can come with challenges that interfere with performance, safety, and efficiency. A skilled pipe gasket manufacturer plays an important role in addressing these issues with custom-engineered gaskets that meet the different demands of each industrial application. Below, our engineers explore some of the most common challenges industrial clients encounter and how a pipe gasket manufacturer provides effective solutions.
High-Pressure Environments
Piping systems in industries like oil and gas or hydraulic manufacturing often operate under extreme pressure. A malfunction or failure in sealing can lead to leaks or equipment damage. A pipe gasket manufacturer offers solutions to this challenge by engineering gaskets with robust materials, such as reinforced rubber or high-performance plastics, capable of handling strong forces. By carefully analyzing pressure ratings and system specifications, a trusted manufacturer can also be confident that the gaskets will maintain a tight seal, even in the harshest conditions.
Extreme Temperatures
From freezing cold water lines to scorching steam pipes, temperature fluctuations can degrade standard gaskets over time, causing them to crack, shrink, or lose elasticity. An expert pipe gasket manufacturer solves this by creating lasting reliability with materials designed for the temperature range of the application. For example, silicone gaskets excel in high-heat environments, while EPDM (ethylene propylene diene monomer) rubber is ideal for cold and UV-exposed settings.
Chemical Exposure and Corrosion
In chemical processing or wastewater treatment industries, pipes are exposed to potent substances that can erode gaskets and cause leaks. A pipe gasket manufacturer solves this by choosing chemically resistant materials, such as fluorocarbons (FKM) like Viton and polytetrafluoroethylene (PTFE), which stand up to acids, solvents, and corrosive agents. By customizing the gasket’s composition, the manufacturer prevents degradation and extends the lifespan of the piping system.
Vibration and Mechanical Stress
It’s very common for heavy machinery and dynamic systems to cause vibration or movement that can loosen connections and wear out seals. To avoid this, manufacturers engineer gaskets with flexibility and durability in mind, incorporating features like compression set resistance or multi-layer construction. These adaptations absorb stress and maintain a secure fit, reducing maintenance needs and downtime for industrial clients.
Regulatory Compliance and Safety Standards
Industries such as food and beverage, pharmaceuticals, and energy are governed by strict regulations that dictate material safety and performance standards (e.g., FDA, ASME and API certifications). A pipe gasket manufacturer meets these requirements by designing and producing gaskets that comply with industry-specific guidelines, so that clients avoid expensive penalties while maintaining safe and hygienic operations. For instance, they might use food-grade rubber for potable water systems or non-toxic plastics for pharmaceutical pipelines.
Customization for Unique or Legacy Systems
Piping system designs can differ—older facilities or specialized equipment tend to require custom solutions. A pipe gasket manufacturer solves this challenge by offering custom engineering services, reverse-engineering obsolete parts, or creating gaskets with precise dimensions and tolerances. This flexibility means that even the most unconventional systems are operational and leak-free.
Partner With a Trusted Pipe Gasket Manufacturer Today!
Choosing the right manufacturer is an important decision for any business relying on piped infrastructure. Whether it’s preventing leaks in a high-stakes oil refinery or ensuring compliance in a food processing plant, Gulf is your solution keeping industries running smoothly.